Engineering (Advanced Engineering)
Data Acquisition and Control
Data acquisition and control system objective is to facilitate integrated operation and control of tokamak and other scientific projects. Assist scientists by providing tools and technique to carry out research experiments planning, operation & control, data archiving and post experiment analysis with ease.
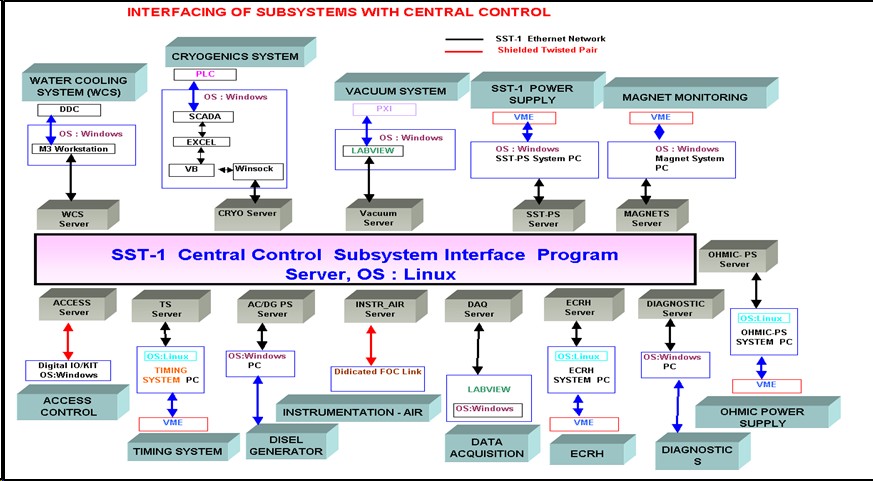
Tokamak Monitoring Software Framework
Software framework for interfacing of heterogeneous distributed tokamak plant systems in order to monitor and orchestrate them for tokamak readiness.
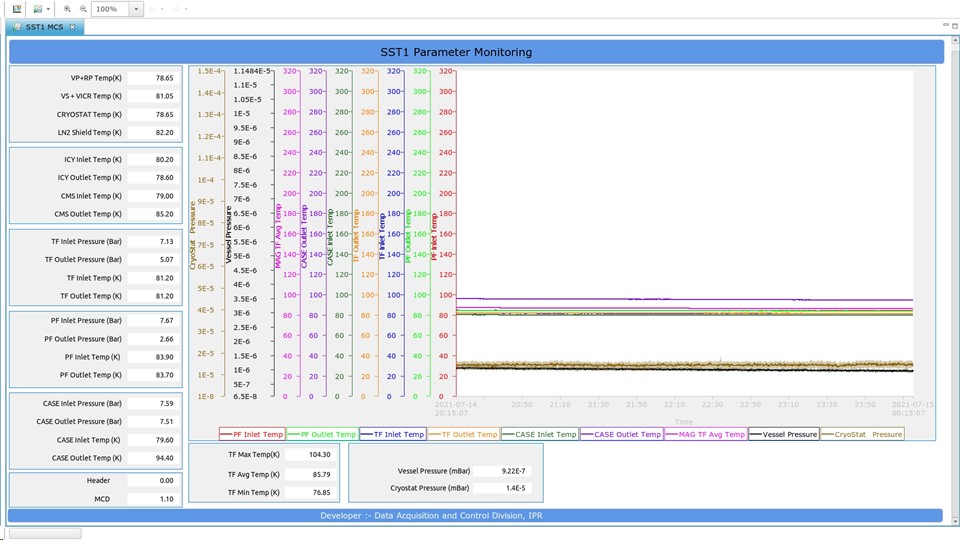
Web Monitoring
Development of web application server for online monitoring of integrated tokamak plant systems from anywhere in the campus at anytime.

Embedded System for Plasma Control
Embedded system for distributed control of tokamak plant system based on VME hardware and real time operating system vxWorks with real time data communication network - Reflective Memory for plasma parameters controls such as position, shape, density and heating.

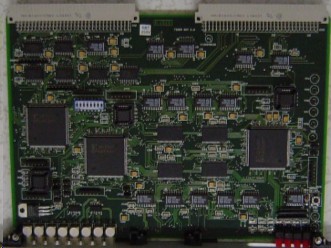
Real Time Event Distribution System
Design and development of VME based time synchronization and event distribution hardware and software for plasma pulse execution. The measured event transmission latency between two farthest nodes of distance 150 meters is 4 microseconds. The timing pulse resolution is 1 microseconds for all the channels.
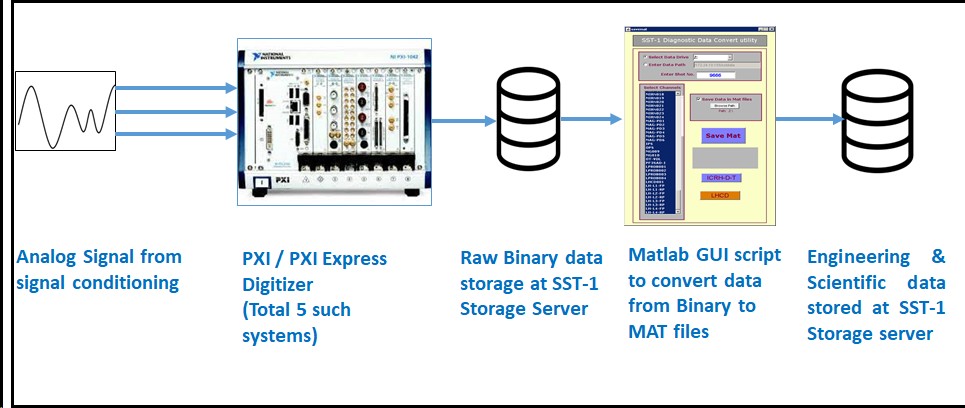
Data acquisition, archive and analysis system
Plasma diagnostic data acquisition system with sampling rates of 10MHz, 1MHz and 100 KHz based on PXIe/PXI and VME platform. Automation of data archiving and backup.
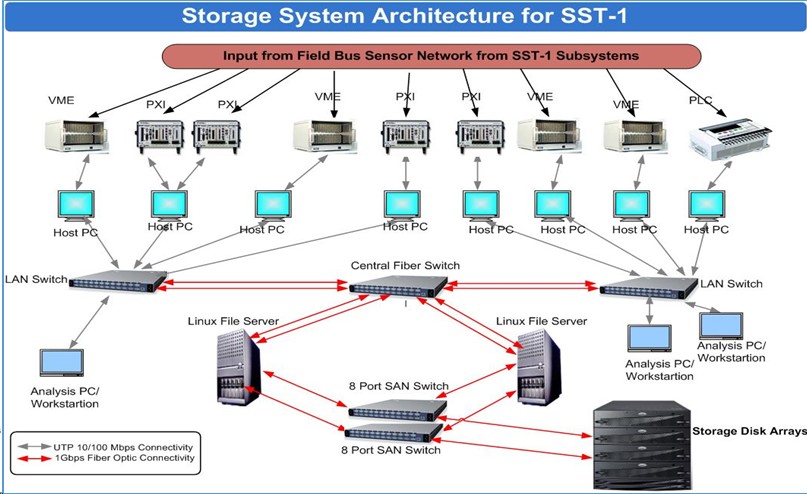
SST-1 Centralized Data Storage
24 X 7 availability of Centralized data storage system for SST-1. The system is based on Storage Area Network (SAN) technology with multi-tier architecture to achieve low latency for frequently accessed data.
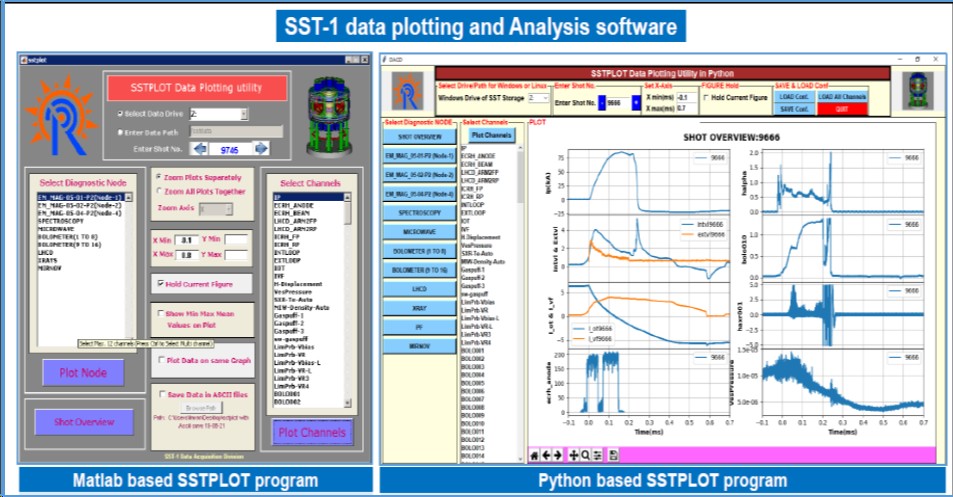
Data Analysis Software
Software for Diagnostic data analysis using Matlab and open source alternative Python
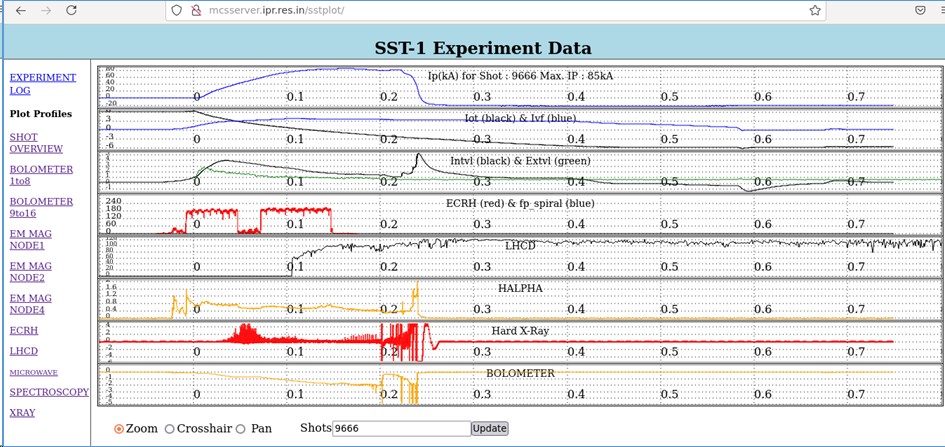
Web based data visualization software
Plasma experiment data are converted into MDS+ tree automatically and are made available for visualization on browser using WSGI technology
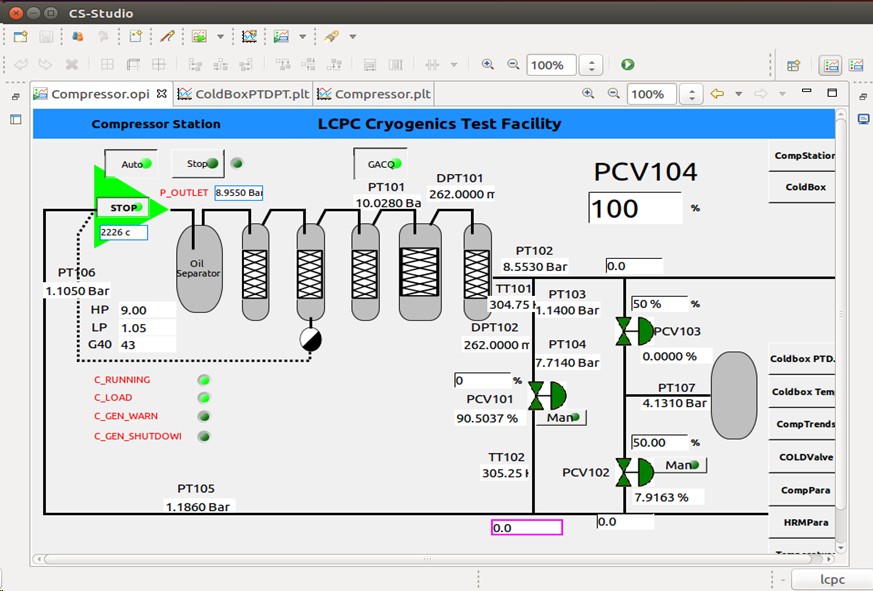
Supervisory Control And Data Acquisition System(SCADA)
Development of SCADA system for Large Cryogenics Plant Control System (LCPC) ) based on open source software framework Experimental Physics and Industrial Control System (EPICS) and Control System Studio (CSS) for various projects
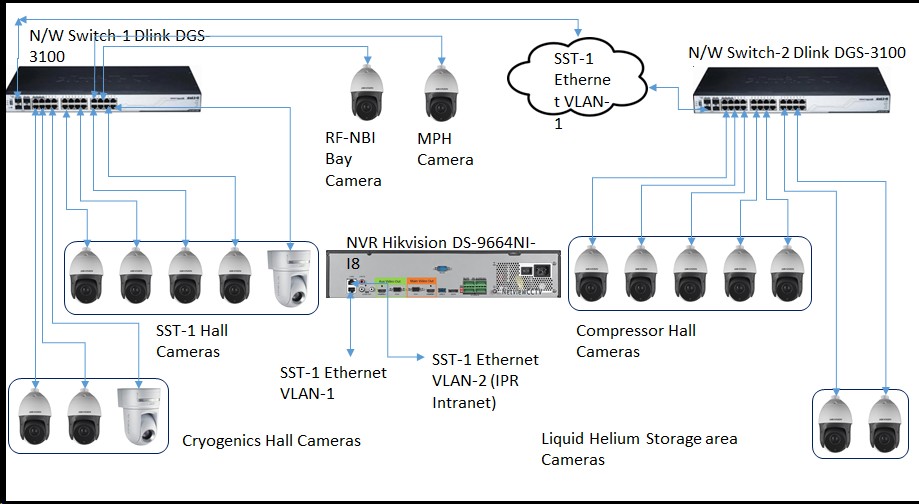
Machine Vision System
Ethernet based PTZ cameras for SST-1 machine monitoring. An optimized video recording is setup based on motion detection. An AI based security system to detect human is already in place. An another application is being developed for the video summarization using machine learning technique.
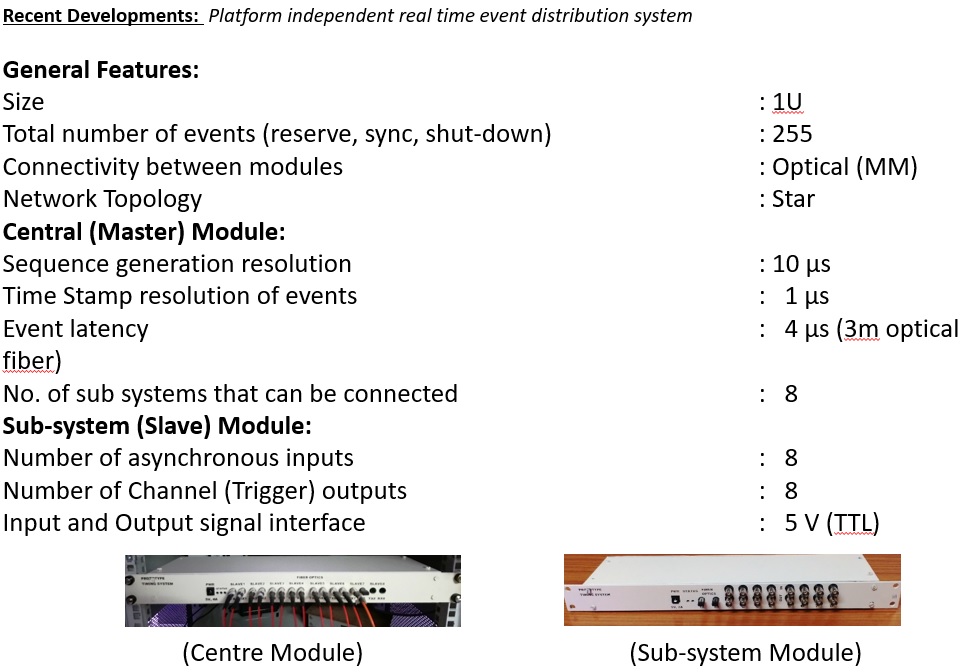
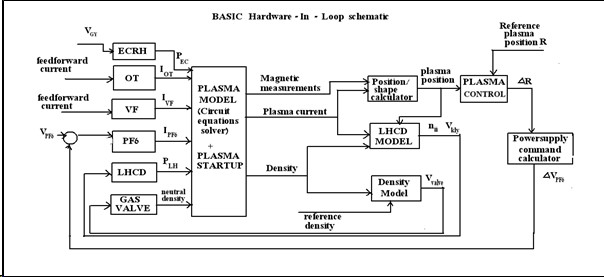
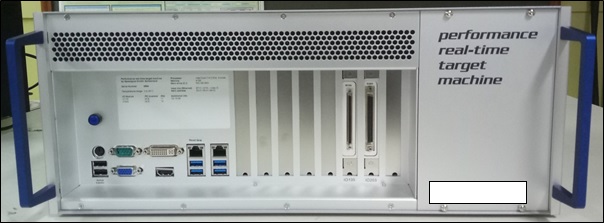
Recent Developments: Hardware In loop for simulation of plasma control model
Hardware-in-loop (HIL) system is widely used for designing the Control Systems.
Requisite hardware has recently been procured and commissioned with SST-1 Operations Division for design of Plasma control System (PCS) which would involve various subsystems providing the real-time control of plasma position, shape and density in a close loop.
Electrical Power Distribution at IPR
IPR Electrical Power Distribution System comprises of 132 kV Substation supplied by a dedicated line from Grid Operator, Uttar Gujarat Vij Company Limited from their Ranasan Substation which is 6 kms away. The 132 kV substation has five step down transformers which bring down the 132 kV supply to 11 kV / 22 kV. All the transformers are of different ratings, ranging from 15 MVA to 37.5 MVA . Three of the transformers are used for experimental loads of ADITYA-U, SST-1 and ITER India Laboratories and Two transformers are used for Utilities. Automatic Power factor compensation system is installed at 11 kV to help correct the excess reactive power generated by inductive loads in the electrical distribution network. With an efficient use of this device, the electrical network can improve efficiency by reducing losses and reduced apparent power demand charges. The Emergency Power distribution System caters electrical power demand from various systems viz. Cooling Water System, Cryogenic and other important safety and investment protection systems. It comprises of 2 x 1.7 MVA Diesel Generator.
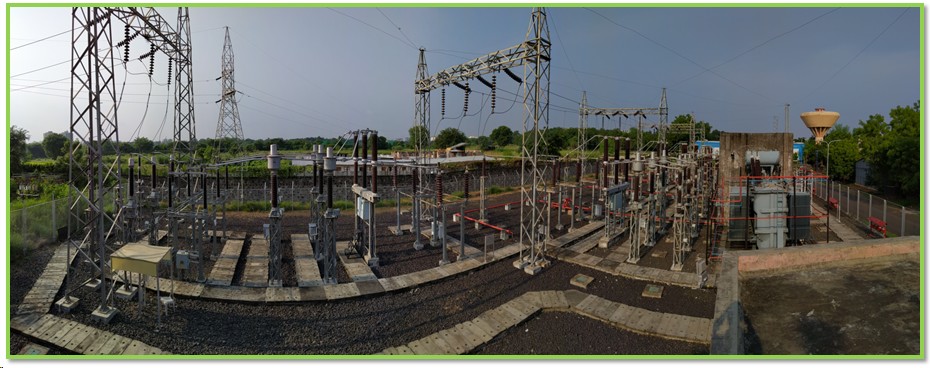
11/22Kv Distribution System:
The 11kV distribution has six 11kV buses to cater various electrical loads while 22kV has two buses to suffice various requirement for ITER India Project’s load.
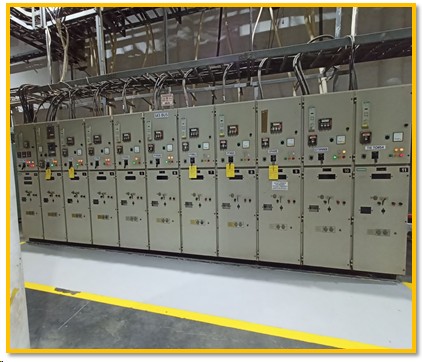
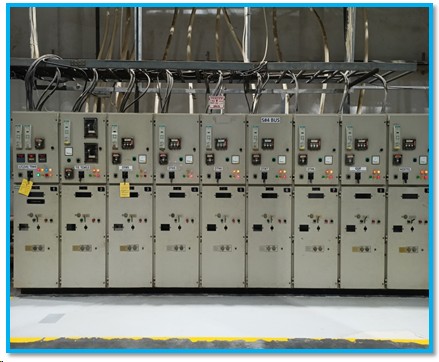
11kV Indoor Distribution
415V Distribution System:
![]() | ![]() ![]() |
415V Outdoor and Indoor Distribution
Power Supplies for ADITYA-U
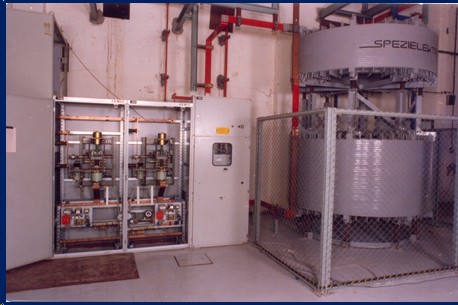
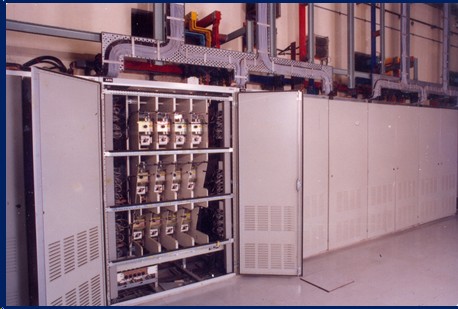
ADITYA/ADITYA-U Tokamak is operated with high current DC power supplies based on the combination of power transformers, line commutated 12 pulse converters, wave shaping circuitry and associated control systems. The subsystem is named as ADITYA/ADITYA-U Pulsed Power System (APPS).
DC Power System: 50 kA Toroidal Field Power Supply, ±20 kA Ohmic Power Supply, 28 kV rated Wave shaper and 12.5 kA Vertical Field Power Supply
Feedback Power Supply (FFPS): 0.25 kV, ±2 kA (Indigenously procured) & Booster Power Supply :2.5 KV (Indigenously Procured)
Coil Power Supplies for SST-1 tokamak
Toroidal Field (TF) , Active Position Control (APC) & Poloidal Field (PF) Power Supply for SST-1 :
TF PS is a 10 kA and 20 V SCR base Converter Power Supply. It is being operated at 10 kA for 3T and 5 kA for 1.5T for SST-1 operations scenarios
APC PS is a 12 kA and 133 V IGBT Based Switched power Supply. It is operational for bipolar current of +/- 6 kA, +/-2 kA during SST-1 operations being used for horizontal plasma control.
PF PS (13 power Supplies) : All the power supplies have a voltage range between 26V to 120 V and current range of 10/20 kA.
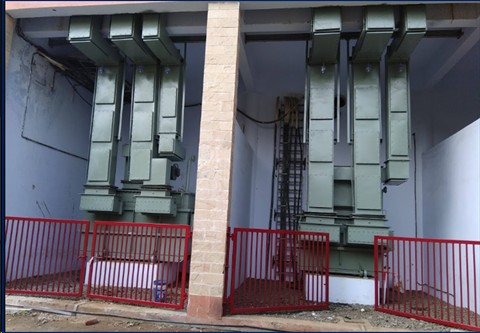
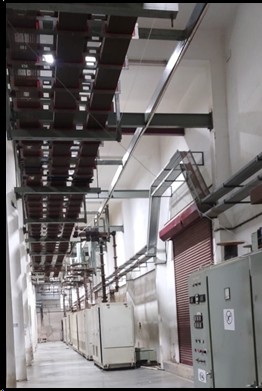
Protection and Measurements
The PF and TF power supplies are scattered from utility building to magnet protection hall (MPH) hall to current lead system. All power supplies use direct current circuit breaker (DCCB) and pyro fuse for protection . In case of any fault DCCB opens and dump resistor is connected in the circuit. Stored magnetic energy of magnet coil is discharged through dump resistor. In case DCCB fails then pyro fuse acts as secondary or backup protection. The dump resistor is connected in the circuit and stored magnetic energy of coil is discharged. Direct current transducer (DCCT) is used for precision measurement. DCCT gives ±10V for ±10 kA current. DCCT provides feedback to the hybrid controller and VME DAC system for realtime storage. Isolator cum earth switch connects and disconnects coil from power supply. The operating parameters of the power supplies are provided using graphical user interface (GUI) software to versa module eurocard (VME) data acquisition and control (DAC) system connected to the power supply.
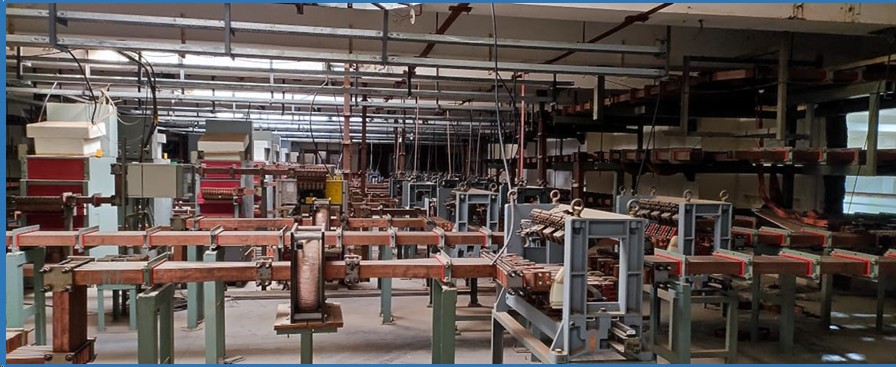
Development of Fast Response Bipolar Power Supply
![]() IGBT inverter power circuit
| Fast response bipolar power supplies are being
developed for Divertor coil of Aditya tokamak
and PF6 coil in SST-1 with rating of 5 kA bipolar,
500 VDC and a fast response of minimum
1 MA/s.Initial results are promising.
The analog controllerhas been developed
in-house.
|
![]() Step bipolar response > 1 MA/s
| ![]() |
Power Supplies for Small Scale Spherical Tokamak (SSST)
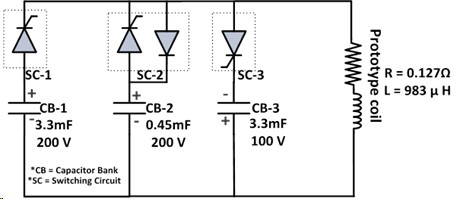
Schematic : Capacitor based Prototype Ohmic Transformer (OT) Power Supply for Small Scale Spherical Tokamak
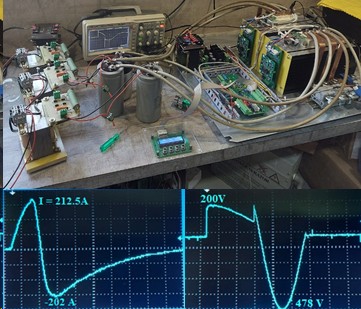
Prototype Ohmic Transformer (OT) Power Supply & Test Results
In the first phase of experiments for SSST there are three power supplies viz.(a) Equilibrium Filed Power Supply (EFPS) (b) Toroidal Filed Power Supply (TFPS), and (c) Ohmic Transformer Power Supply (OTPS). The conceptual design, simulation and analysis for all these three power supplies have been completed successfully. The Prototype power supply for Ohmic Transformer System has been developed and tested successfully. The development of prototype power supply for Toroidal Filed Coil is in progress and in fabrication stage. Apart form the prototypes, the actual power supplies for SSST are in the procurement and manufacturing stages in the development ladder.
Electronics & Instrumentation
Electronics & Instrumentation Division develop customized front end electronics, indigenous data acquisition systems, timing & control systems and automated control systems required for various physics experiments in Institute. Various signal conditioning units have been developed to measure signal of sensors for determining plasma parameters like current, temperature, density etc. The electronics has been designed to achieve compact size, low power and immunity from high electric and magnetic field of Tokamak. As per experiment requirement specialized analog integrated chips, data converter, memory chips, microcontroller, digital signal controller, FPGAs and System on Chip are used for signal conditioning, processing, acquisition and control applications. Around 400-500 nos. of modular electronics boards with various functionalities are operational in Institute.
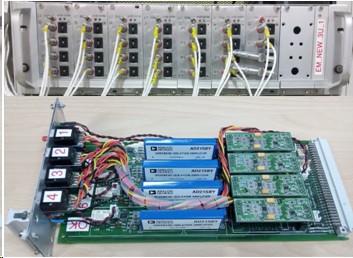
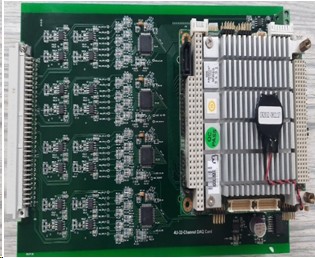
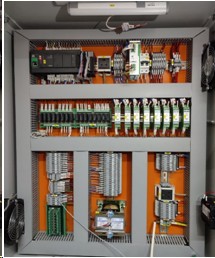
Electronics Division developed Plasma Diagnostics Electronics, Data Acquisition, Timing & Control Systems for Aditya-U Tokamak.
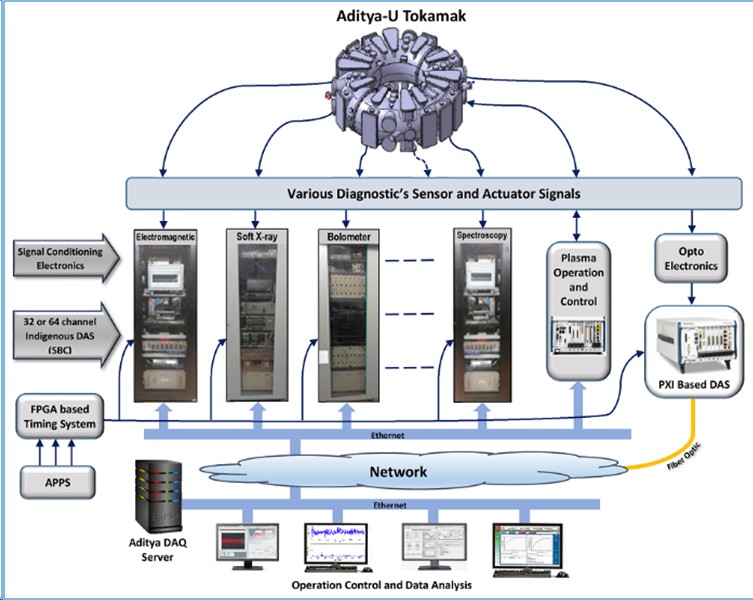
Trigger and timing control system for ADITYA-U
The trigger and timing control system has been developed and installed in ADITYA-U Tokamak for synchronization of the data acquisition system and TFPS along with wide spread diagnostic systems. Total 52 such channels are installed in ADITYA-U. Either electrical signal or optical signals can be interfaced as input signals. Presently 3 optical signals coming from TFPS and 2 electrical signals are taken as input signals. Any of these input signals can be taken as a reference signal and with respect to it a pulse can be generated at any of the output channels with the variable delay. The reference input channel and delay can be remotely set through PC using LabVIEW based graphical user interface.All the output channels are electrical signals and isolated with each other.
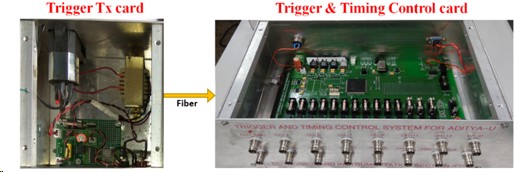
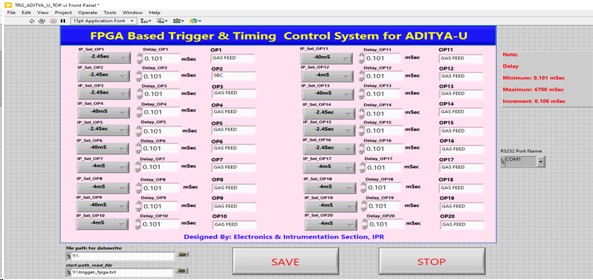
Key features:







Data Acquisition System for Diagnostics
Electronics and Instrumentation Division has indigenously developed a customized data acquisition system to acquire data of Plasma Diagnostics signals. Two different versions are developed as per the experimental requirements, SBC-64 for 64 inputs and SBC-32 for 32 inputs. This system with on-board computer can acquire analog signal within range of +/-10V at sampling rate of 250KSPS for shot duration of 500 mS.
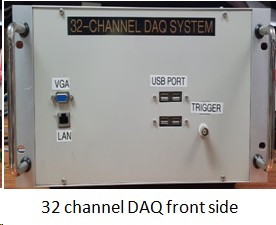
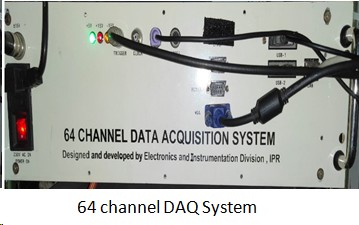
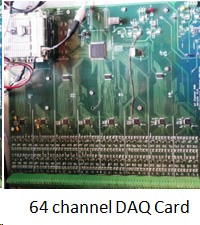
Programmable Automation Controller
To cater various needs of IPR experiments, we developed high speed controller employing latest generation of FPGA. The FPGA also has on chip soft processor block, which can perform slower sequential tasks. This board is used for multiple experiments of the IPR Lab in RF source control and Degaussing Control System.
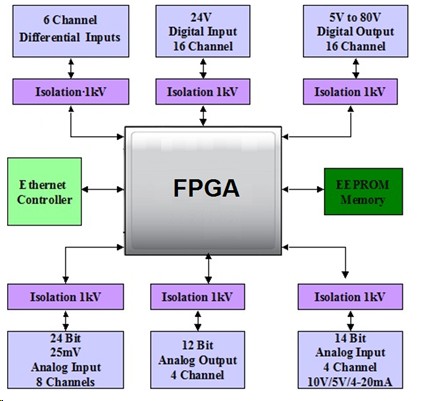
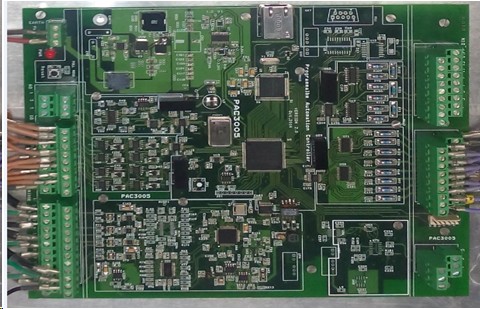
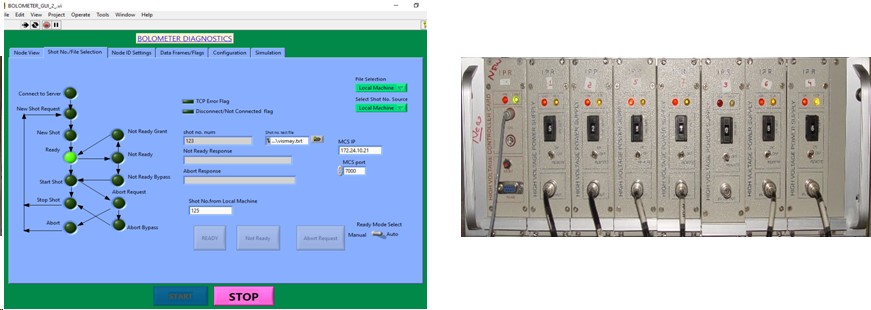
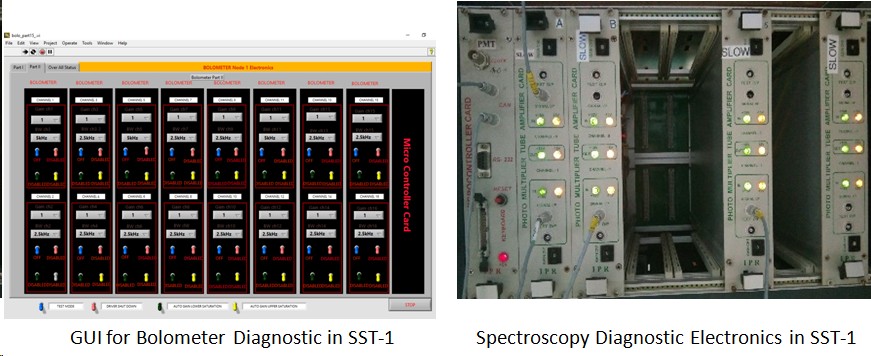
Various signal conditioning electronics has been developed to interface different diagnostic sensors like AXUV diodes, photo multiplier tubes, magnetic probes and coils and Langmuir probes etc. to measure different parameters of plasma. The parameters of electronics is remotely controlled with LabVIEW
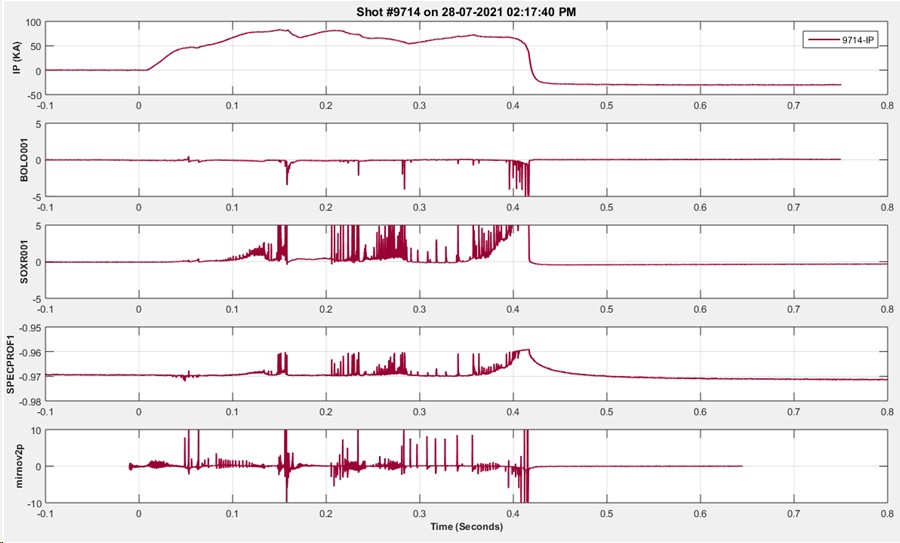
EM Diagnostic Signal Conditioning Electronics with Data Acquisition System
The customized signal conditioning, acquisition and power supply has been integrated in single sub-rack chassis. The system is developed with Zynq SoC FPGA as main controller. The ARM processor of the SoC communicates with the host computer over 1G Ethernet. The signal condition card has 5kV isolated analog amplifier with 4th Order analog filter to extract signal from the probe coils. All the power rails needed to power the DAQ and electronics are also onboard.
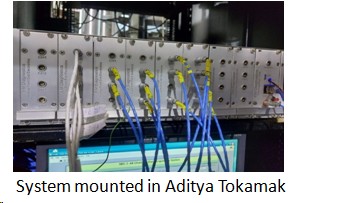
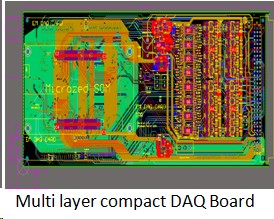
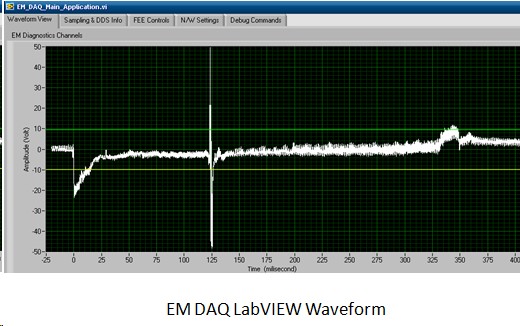
Integration of DAQ with signal conditioning eliminated need of long wiring from signal conditioning chassis to DAQ chassis.
Development by Electronics and Instrumentation Division
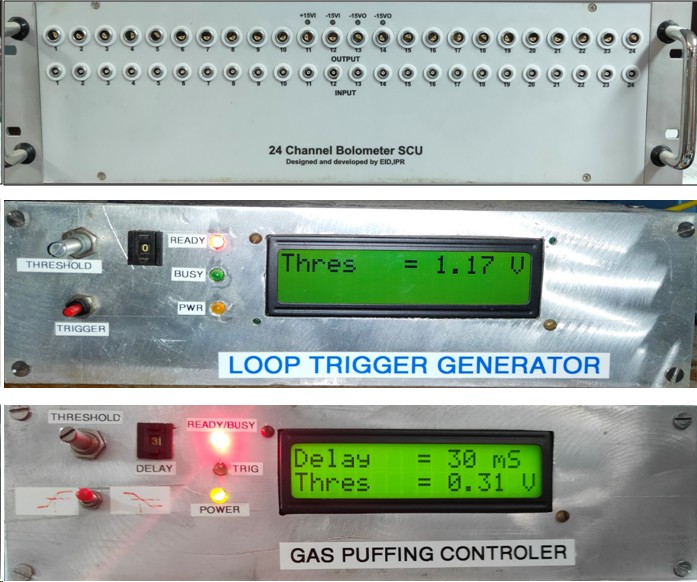
Front end Electronics for Langmuir Probe
An electronic system for the sweep generator and temperature measurement, floating Potential and density measurement is developed for Langmuir probe diagnostic in Aditya-U and SST-1. The system of temperature measurement comprises of low-voltage sweep generator, high-voltage amplifier, power–supply modules and the measurement circuit, all mounted in a single chassis.
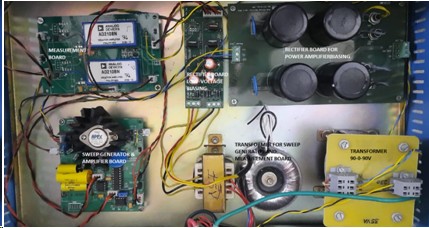
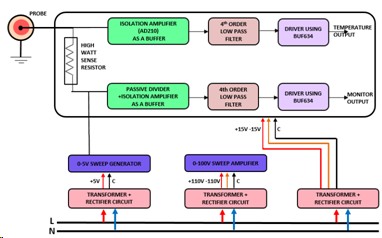
![]() ![]() ![]() | ![]() |
DSP Real time control Applications
TMS320 series controller based circuit of different real-time processing applications; two such applications has been installed, one installed application is for real-time plasma position calculation and obtained good results which is compared in the below graph., second implemented application is hysteresis band controller for in-house development of HV power supply. The TMS controller runs at 150MHz and a floating point operation can be done less than 20ns. This development found very useful for different feed-back control applications in Aditya and other Labs.
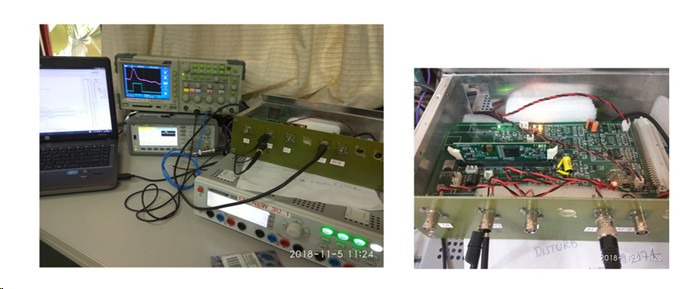
Automation & Control Systems
Aditya Vacuum Vessel with Heaters
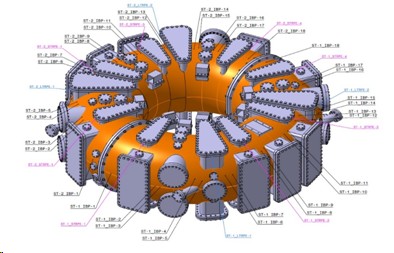
Semi Torus 1 Monitoring Screen
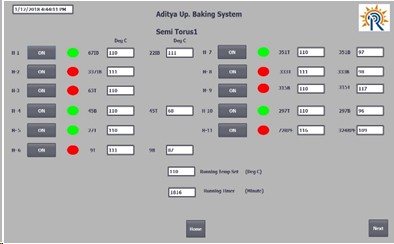
Automation of Baking Control System for Aditya Upgrade Tokamak:
Baking of vacuum vessel and first wall components is a prerequisite in order to obtain impurity free plasmas in the upgraded ADITYA-U tokamak. The baking control system consists of 80 heaters, RTD installed on different sectors of the vessel, pumping lines and diagnostics.
The heaters are controlled in close loop by in-house developed control system using Siemens PLC, SCADA, SSR, electrical switching & protection.
The control cycle comprises of three main phases, temperature ramp-up, and constant heating and ramp-down to room temperature.
The baking control system is operating successfully for its automatic operation and long operation hours (48 hours) at 135 °C for last four years.
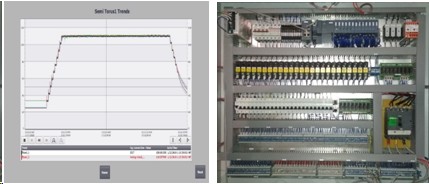
Semi Torus 1 Temperature Trend Baking Control PLC Panel
Aditya Capacitor Bank Automatic Charging System
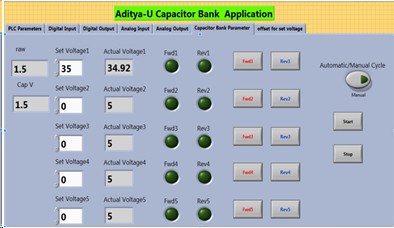
Wago PLC programmed with Codesys software
SMARTEX Plasma Baking Control System
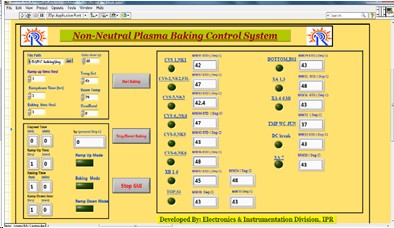
Schneider PLC programmed with Somachine software
SST-1 Hydrogen Pellet Injection System
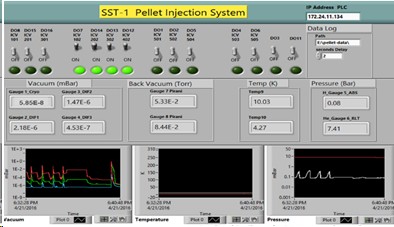
Siemens PLC programmed with TIA portal software
ECE Black body Heating control System
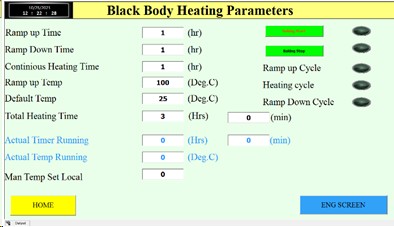
Phoenix PLC programmed with PC worx software
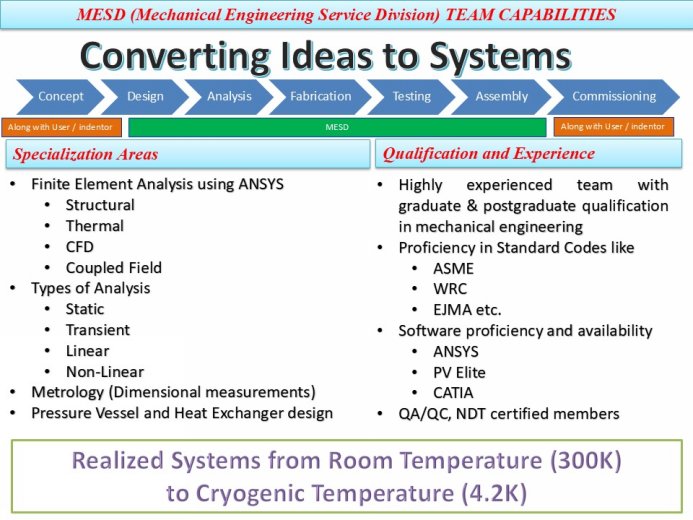
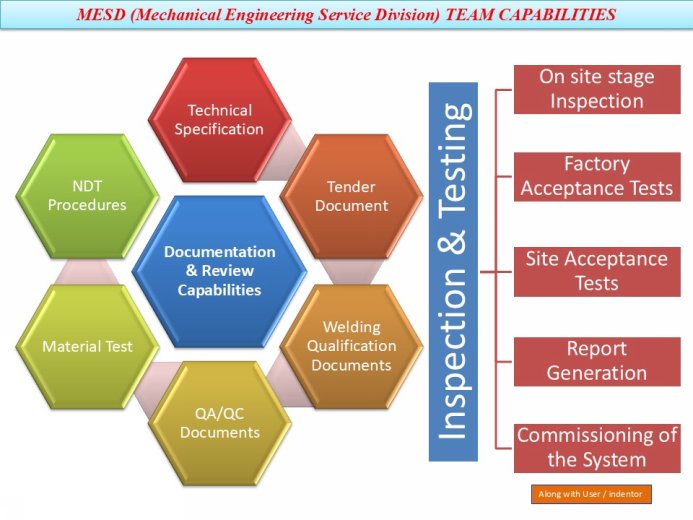
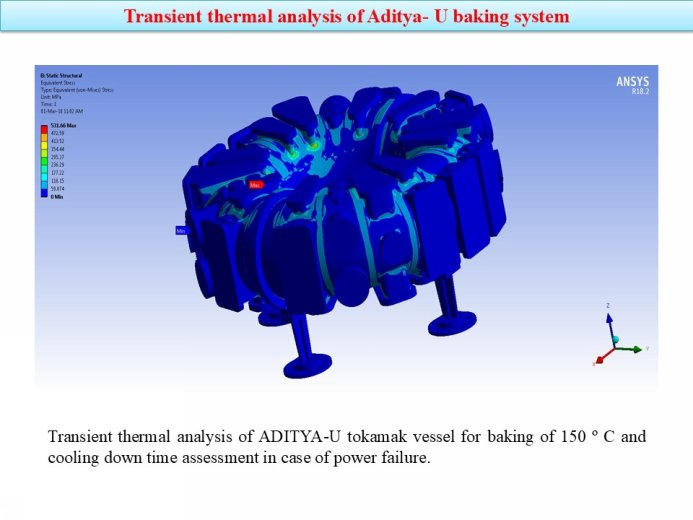
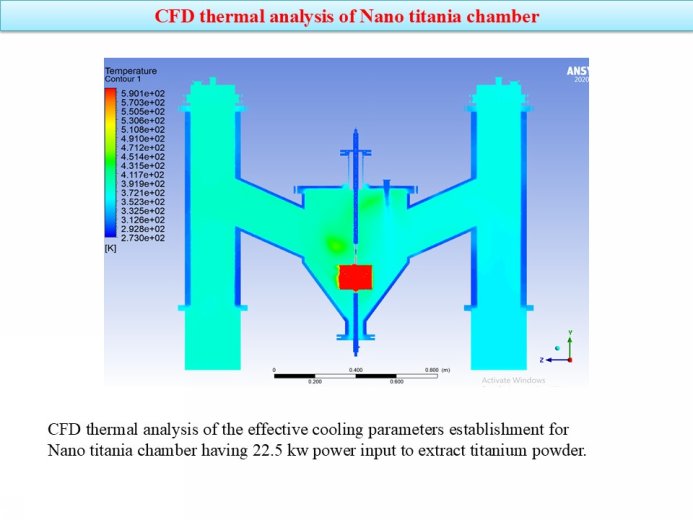
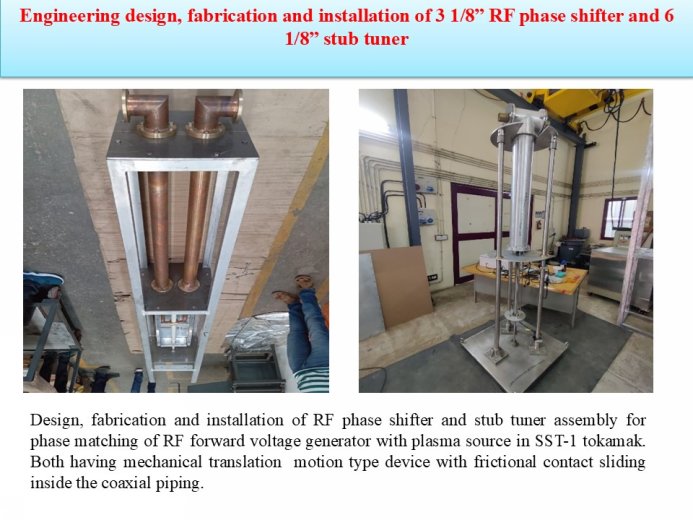
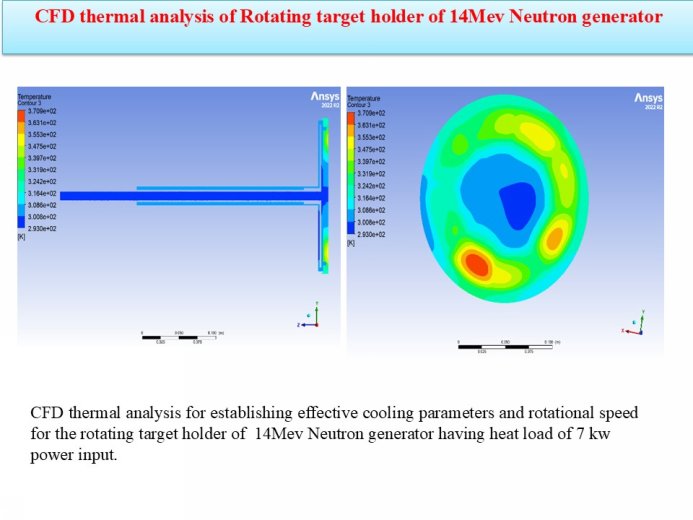
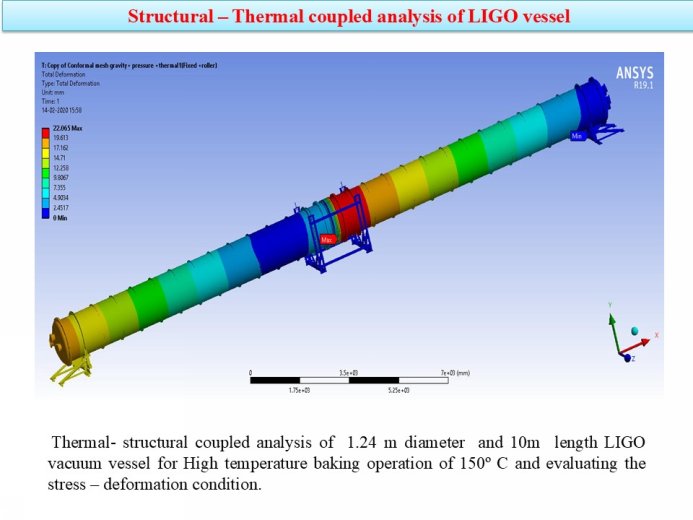

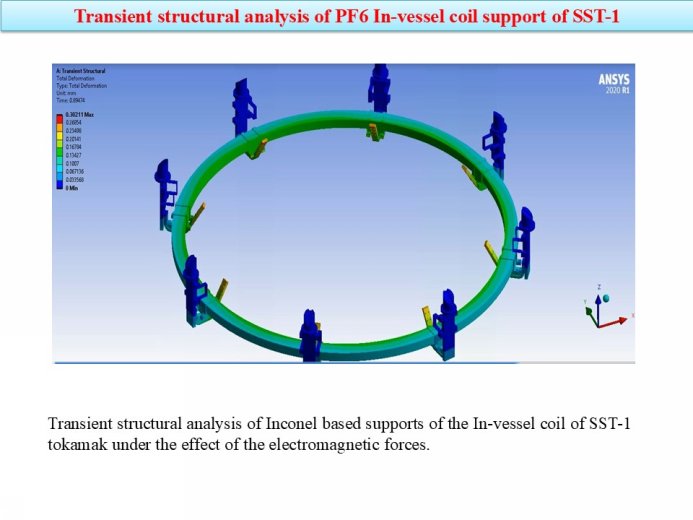
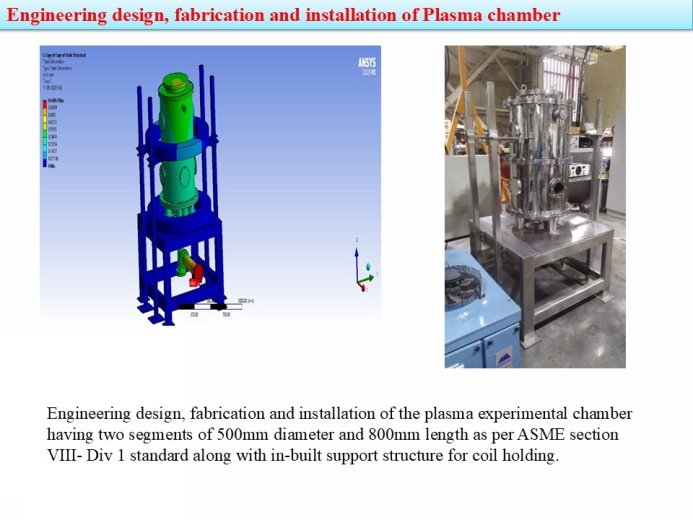
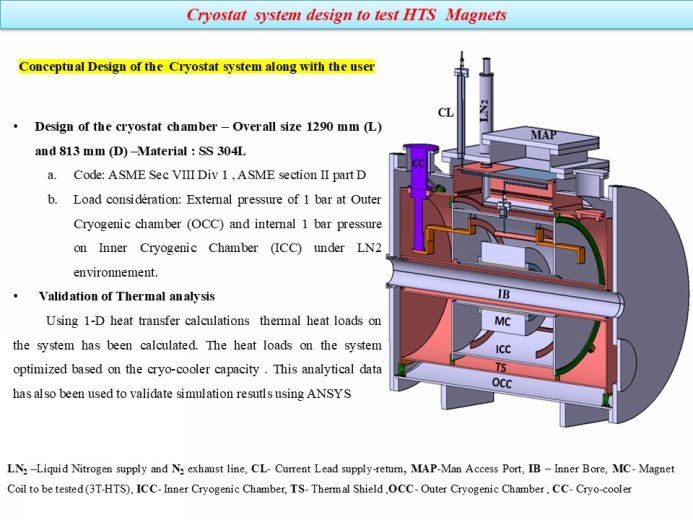
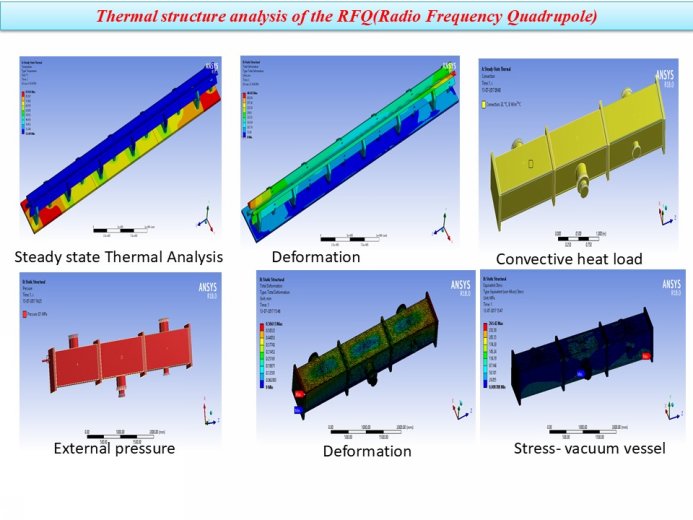
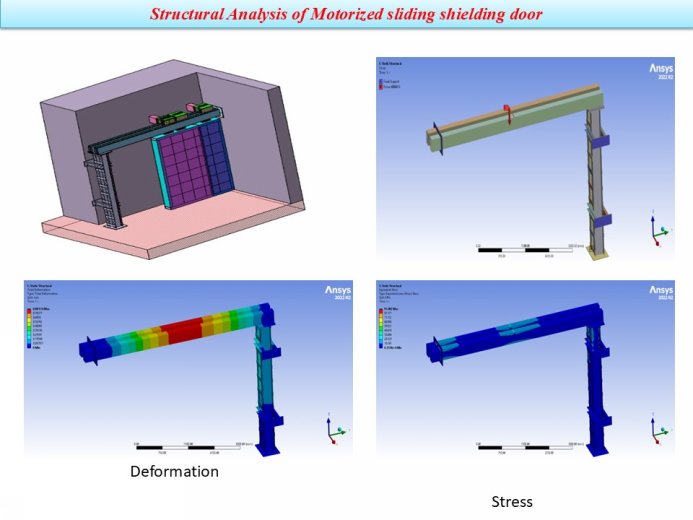
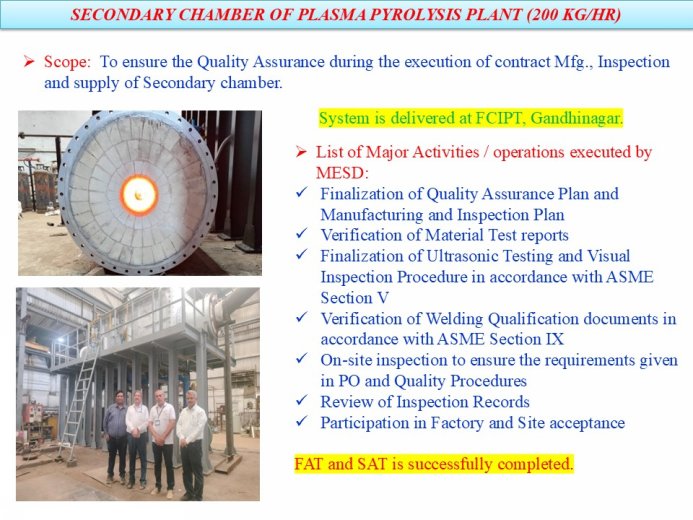
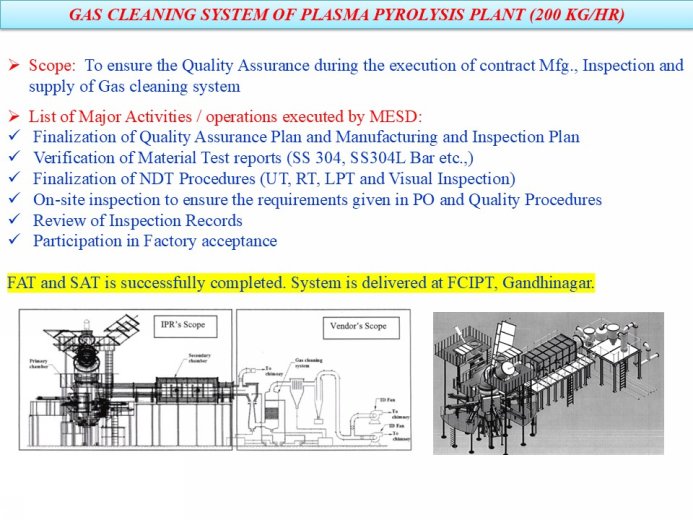
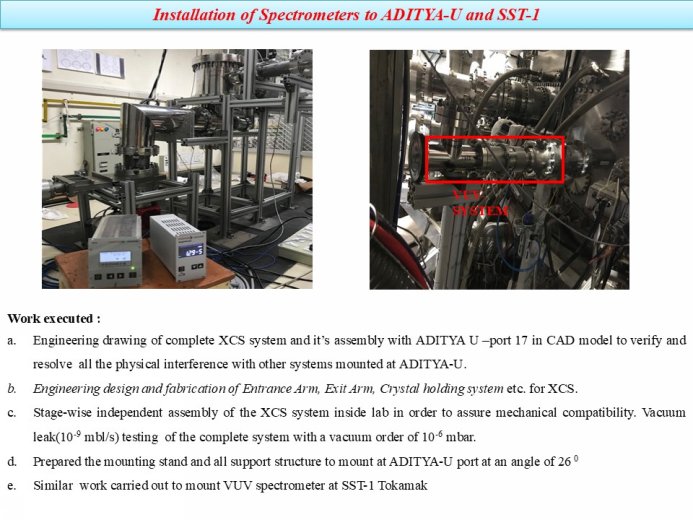
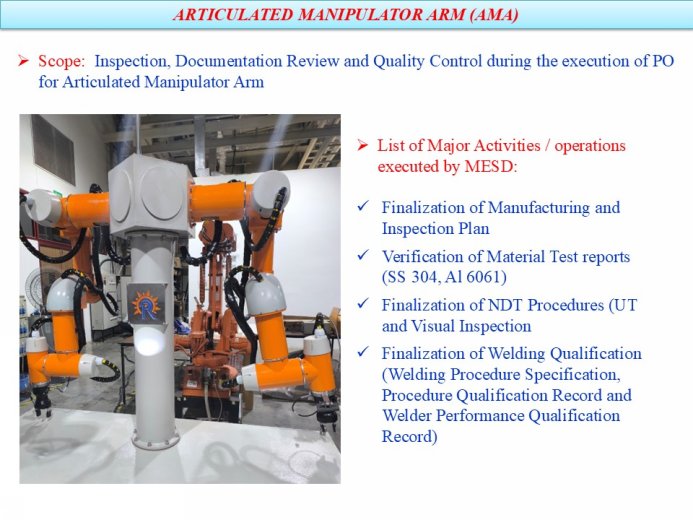
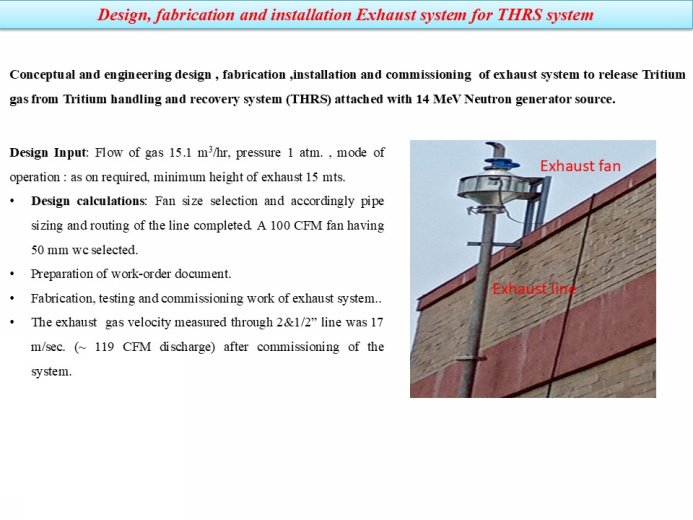
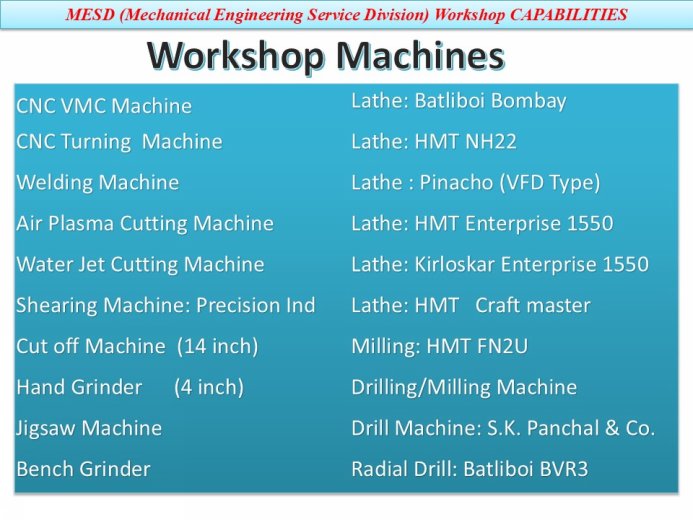

- Data Acquisition & Control
- Electrical Power Supplies
- Electronics & Instrumentation
- Mechanical Engineering
- Vacuum & Surface